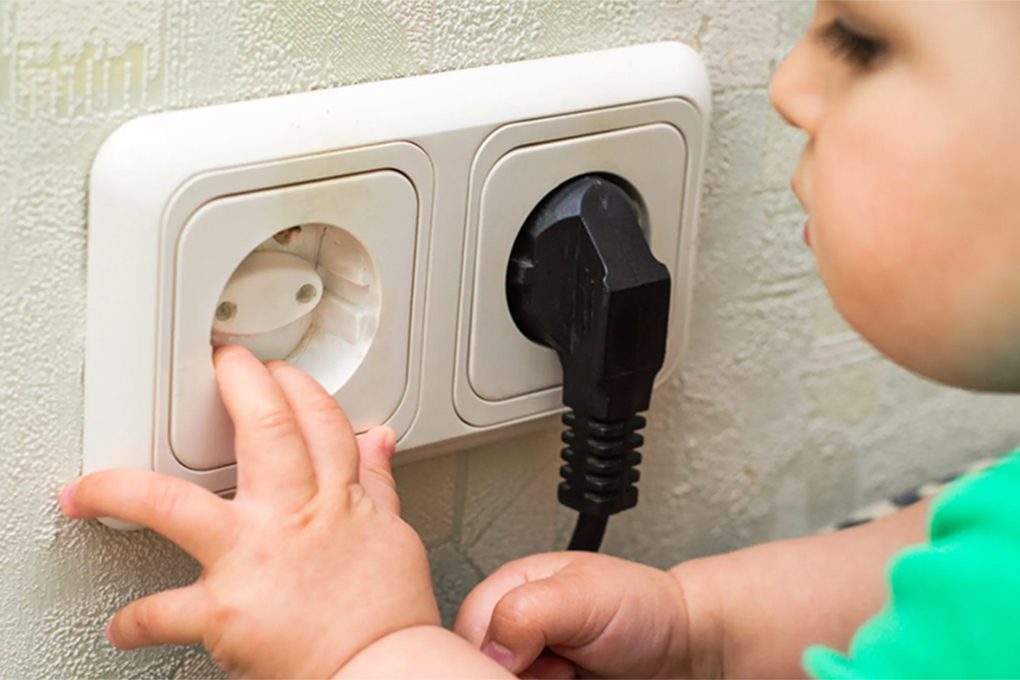
What is Poka-Yoke?
Do you know what Poka-Yoke is? It is one of the most effective methods of work standardization that can be used in any organization.
Lean Management adopted various principles and methods that originated as part of the Lean Manufacturing methodology, and Poka-Yoke became one of the most effective methods of work standardization, applicable in any sphere of production or services.
The idea used in this method, the prevention of errors and defects, is very versatile and has proven its effectiveness.
Meaning and Origin of Poka-Yoke
The term Poka-Yoke (ポカヨケ, poh-kah yoh-keh) was coined in Japan in the 1960s by Toyota industrial engineer Shigeo Shingo. Shingo also developed and formalized Zero Quality Control, a combination of Poka-Yoke methods to rectify potential defects and check the source to prevent defects.
Initially, the term was pronounced as “baka-yoke,” meaning “protection against foolishness,” but it was later changed due to offensive connotations. Poka-Yoke now means “error-proofing” or, more literally, the prevention (yokeru) of unintended errors (poka).
Poka-Yoke ensures that the correct conditions exist before performing a step in any process, primarily preventing the occurrence of defects. Where this is not possible, Poka-Yoke serves a detective function, eliminating defects at the earliest stage of the process.
Poka-Yoke is any mechanism in a lean production process that helps avoid mistakes. Its goal is to eliminate product defects by preventing, correcting, or drawing attention to human errors as they occur.
Examples of Poka-Yoke Application
In a broader sense, this is also a constraint defining behavior, like a step in a process that prevents incorrect work.
One of the most common examples is a driver of a manual transmission car having to press the clutch pedal (a process step – Poka-Yoke) before starting the engine. The interlock prevents unintended movement of the car.
Another example is an automatic transmission car with a selector that requires the car to be in “Park” or “Neutral” before starting.
They act as constraints defining behavior because there are actions that must be performed before the car is allowed to move. Over time, the driver’s behavior adapts to the requirements through repetition and habit.
Other examples can be found in childproof electrical outlets or a washing machine that won’t start unless the door is properly closed to prevent water leakage. These types of automations do not allow errors or incorrect operation from the very beginning.
In Summary
The Poka-Yoke technique is one of the most valuable gems in the crown of Lean Management. It is a way to ensure quality without the actual quality assurance process, primarily aimed at preventing defects.
Poka-Yoke can be implemented in any industry and has numerous advantages, the most important of which are:
- Helps get it right the first time
- Over time, makes errors impossible
- It is cost-effective
Errors are normal; just don’t repeat the same mistake again and again. To avoid repeating the same mistakes, specific checks or procedures need to be implemented, and that’s where Poka-Yoke techniques come in.
Tag:Agile, Project, Terminology